There are two ways to improve your business operations. 1) You can fix problems and 2) You can raise the current standard.
Lean management is all about continuous improvement. But using a Problem solving methodology sometimes can fall flat when you aren’t actually solving a problem, and you’re simply trying to make an improvement to the current status quo.
So, let’s briefly look at the difference and dive deeper into how to identify problems, or improvement opportunities.
Problems vs Improvement Opportunities.
In my article on the difference, I go into more depth. But basically, a problem exists when you aren’t performing to the level or standard you are expecting for that process or output. And, an improvement opportunity is when you identify a possibility of raising the standard.
Simply put, a problem exists when there is a gap between what should be happening, and what is actually happening.
An improvement opportunity exists when what should be happening is what is actually happening. But you think you can make what should be happening (and what is actually happening) even better for you or for the customer.
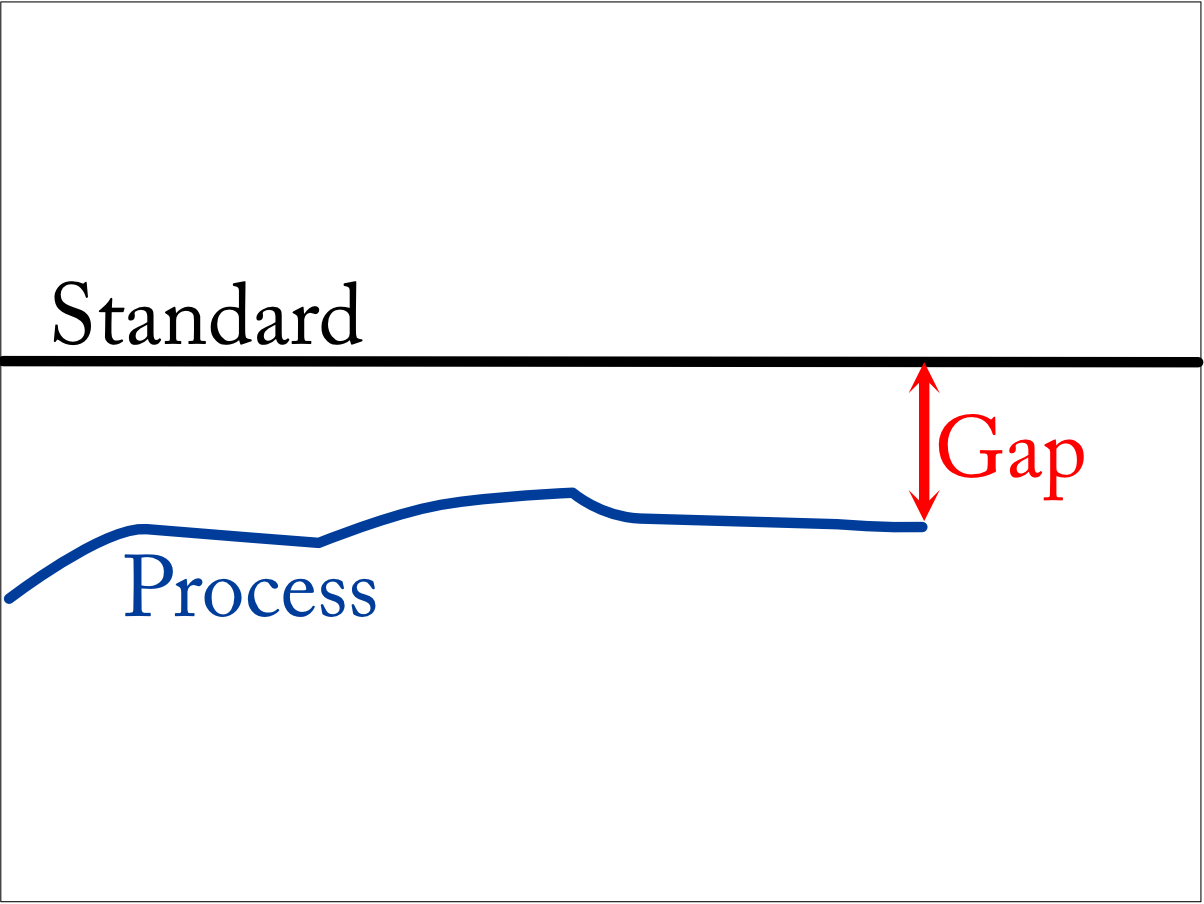
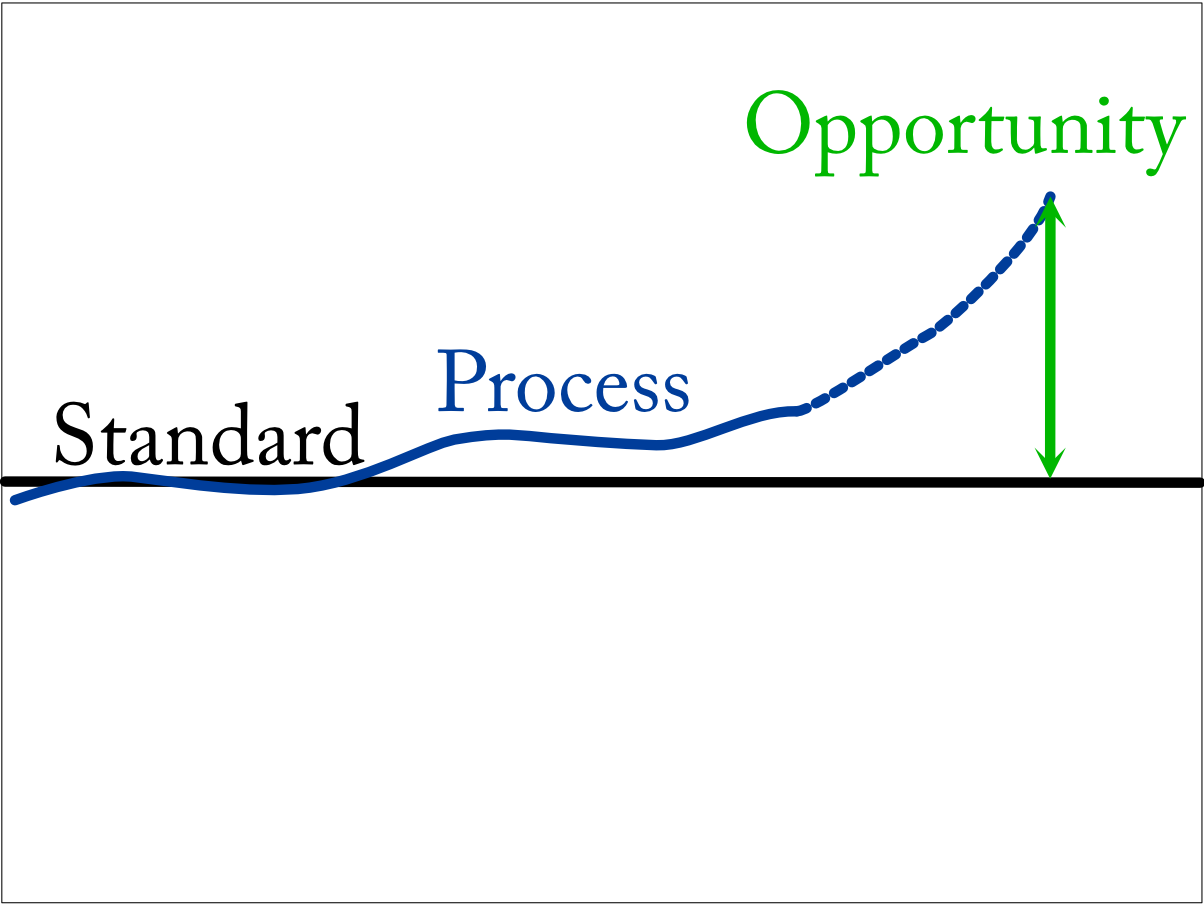
Identifying Problems
As stated, a problem is a gap between what should be happening and what is actually happening. So, you need to know two crucial pieces of information in order to identify problems.
First, you need to know what should be happening. This is all about having set standards.
In my article on standards, I mentioned that for the most part, you only need to set standards on what is critical to your business. Those things that are really important.
And Standards are measurable. If you can’t actually measure your standard, you can’t check to see if you are meeting it, or if you have a problem.
The second thing you need to know is what is actually happening. In order to know what is actually happening, you need to have some way to measure your current state. And, you need to take those measurements often enough to know whether you’re consistently performing to the standard or below.
I suspect that many of you reading this are thinking “It’s so much work to track these _____ every day!”
You may even accompany that sentiment with an angry face 😡.
I get it. This is why this only should be done on procedures or outputs that are critical to your business. The old adage of “It’s better to have it and not need it, than need it and not have it.” doesn’t always pertain to this. Especially when getting the data takes a significant amount of time. Time that could be spent working on critical money making aspects of your business.
There are also MANY ways to track things and ideally you will find what is best for you, your space, your working style, and your process.
So, keeping in mind that you are only tracking critical information, how much do you need to track?
Well, a single data point does not a trend make.
If you are, for example, tracking the time it takes to do a repetitive task, and you measure that time once. That’s not a trend, It’s one data point. There’s no way to know if you always average about that time. Or if that was one way off data point and you usually take half the time or twice a long.
You need a minimum of 3 data points. More is usually better.
I’m not a data zealot. I won’t tell you that you have to have a statistically significant number of data points. While, for some operations you do. (If you are working in pharma, or are manufacturing equipment that will at some point be used in a way that could affect human safety, yes, you need a statistically significant amount of data. If you’re tracking the time it takes for you to write a blog post, you’re ok with a few data points provided the content is about the same length and type.)
Examples of Problems
Let’s look at some examples.
Ok, so I already mentioned blog post writing, so let’s take that as an example first.
You have many different ways you can measure your process for blog posting.
Maybe you want to track the time it takes you to write a post, maybe your actual publication process isn’t that complicated, you just write, and hit publish. So, in this case, words per minute, or words per time block, could be a good measurement. Just tossing numbers out here, maybe your standard is 500 words per 25 min pomodoro. If you make more than that, fine, but if you always hit less, then perhaps something needs to change.
Or, maybe your process is complicated and writing is a smaller portion of preparing and publishing an article. Maybe you need to count the number of time blocks you use to post an article. This could very well be the case if you have to take or find photos and upload them and make sure they make sense in the layout of the article.
Either way, you will need a way to track your current state. In the words per time case, you can time yourself working (start and stop) and just write down how many words you wrote. A little math in a spreadsheet can help you calculate your words per min. Or you can do words per time block and at the end of each working time block you mark the number of words written. Then it’s a really simple thing to see how you’re performing with respect to the standard.
If you’re counting time per full post, you may need to keep track per each article written. For example, maybe it takes 2.5 pomodoros that you’re using as 25 min each for an article. Then another article might be 2 pomodoros. You can compare that to your standard. Maybe your standard is 3 pmodoros. Anything under that is good to go, but if you keep creeping over that maybe something needs to change.
Tracking
There are many ways you can track your standards and your performance against those standards.
Always, my preferred way is visual.
There’s this concept in Lean known as the 5 feet 5-second rule.
Can you stand 5 feet away and get the information you need in under 5 seconds?
Obviously, we aren’t all working in manufacturing-type situations.
But if it takes longer to decipher the information than about 5 seconds, it’s too complicated.
Imagine this: A magnetic board with a line horizontally across the middle.
Under the line is shaded green. Above the line is shaded red.
The line is your standard. 3 pomodoros per article.
Then, you can divide the board into vertical columns. Each column representing an article. Every time you publish an article, you place a black marker on the board at the level corresponding with the number of pomodoros it took. Over time, you’ll see the trend. Maybe sometimes you go over, and maybe that’s OK, but if you’re always going over. Then you know you have a problem.
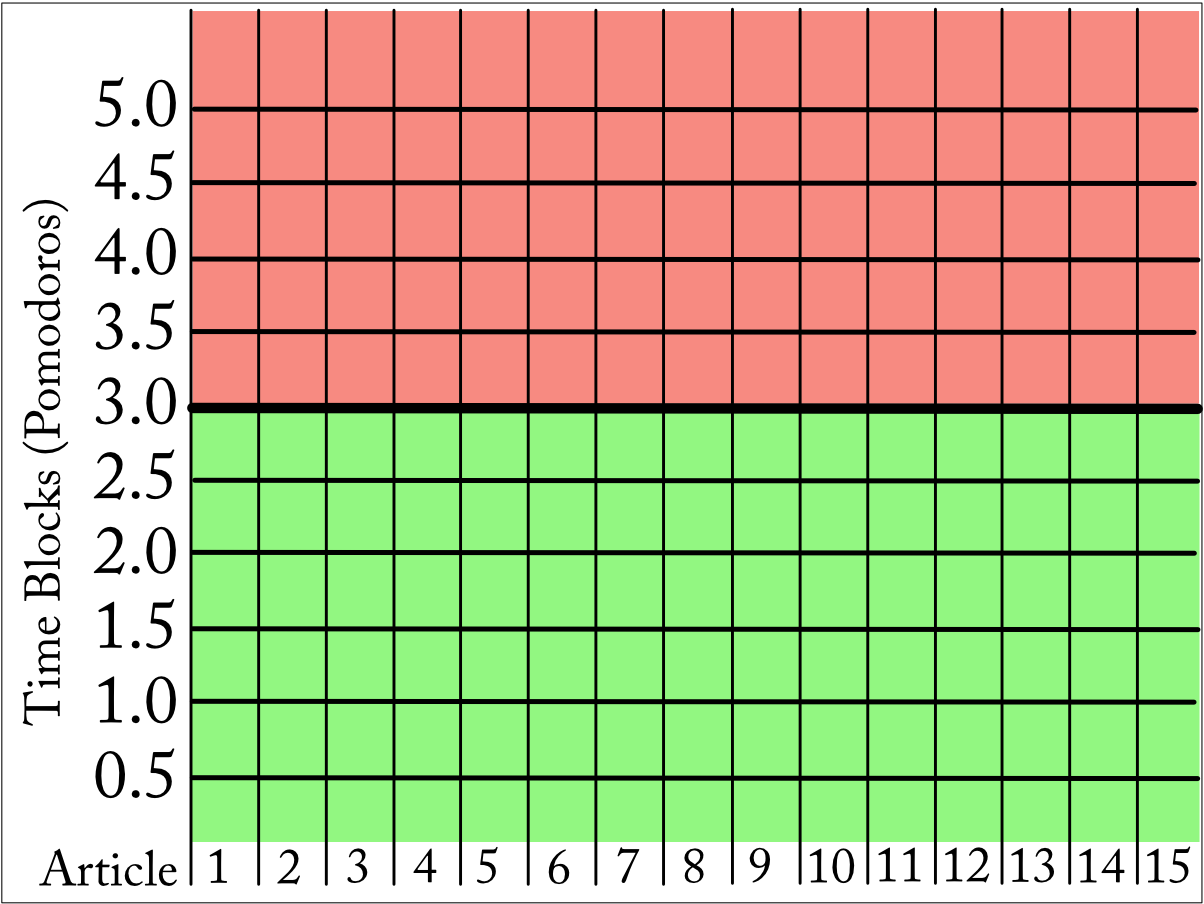
Incidentally, if you are tracking words per minute, you’d want to reverse the board, the lower numbers would be shaded red, and the higher numbers green.
Can you do this electronically? Yes. You could set up a spreadsheet and just mark Xs.
Or, you can do a conditionally color-coded column or row where you type your number in.
Regardless of how you do it, you shouldn’t have to do complicated math to really SEE if you’re meeting the standard or not.
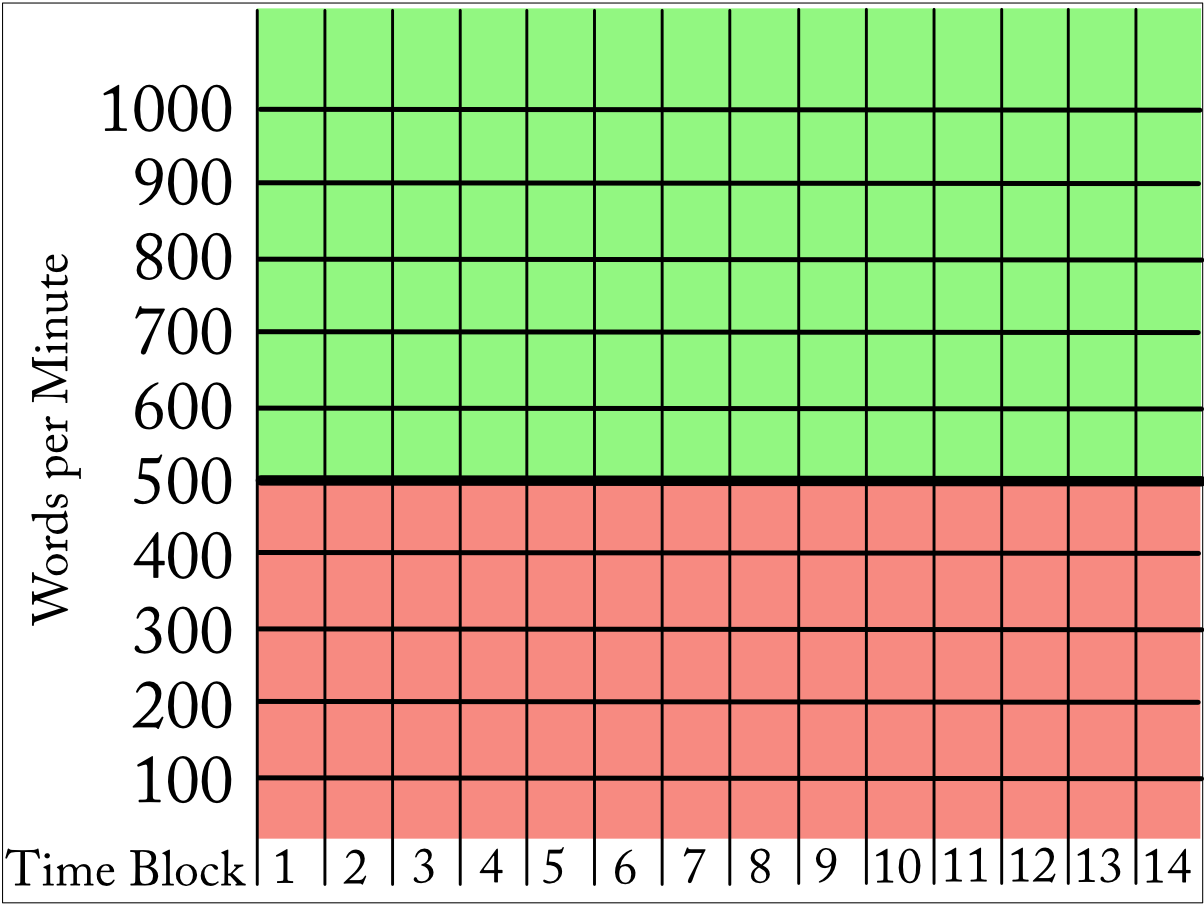
Identifying Improvement Opportunities
Problems should be super simple to spot. (The solutions aren’t always easy, but finding the problems should be.)
However, identifying improvement opportunities might not be that straight forward.
Or, it could be.
If you are tracking something, say number of pomodoros that it takes to publish an article, and you notice that you are consistently hitting REALLY close to 2 when your current standard is 3. You have an “improvement opportunity”. Really, that’s improving your standard to 2 per article.
However, maybe you are doing 3, and you feel like if you switched some things up, like the way you processed photos, or if you learned a different software for editing photos or a different theme for laying out the post you could drop it to 2. That also is an improvement opportunity.
Some times you just feel like you can do better, even if you don’t know that you can. It’s an improvement opportunity, even if you don’t know how you get there. Or how far you can go.
Conclusion
It may seem obvious, but there is a difference between a problem and an improvement opportunity.
Both imply that you know your current standard and how you are performing against that standard.
But, if your standards are set such that you know you need to meet or exceed the standard in order to achieve your business goals, then it’s advisable that you work on solving your problems first so you can continue to make your goals.
Of course, if you have an improvement opportunity that could bring you in millions of dollars and fixing your problems are just going to make your life a little easier in the short term, go for the improvement!
Both problem solving and improving the standards are part of the continuous improvement ecosystem.