There’s a saying in Lean that: No Problem is a Problem.
What they are saying is Having No problems … is a problem. Which doesn’t make sense does it? Why would I want problems in my business?
Well, you don’t.
But, if you have problems, then you can fix them, and therefore you can make improvements and get better.
Lean is all about continuous improvement.
Do any businesses REALLY have no problems? No…. No they don’t.
What is a problem? A problem is a gap between what should be happening and what is actually happening.
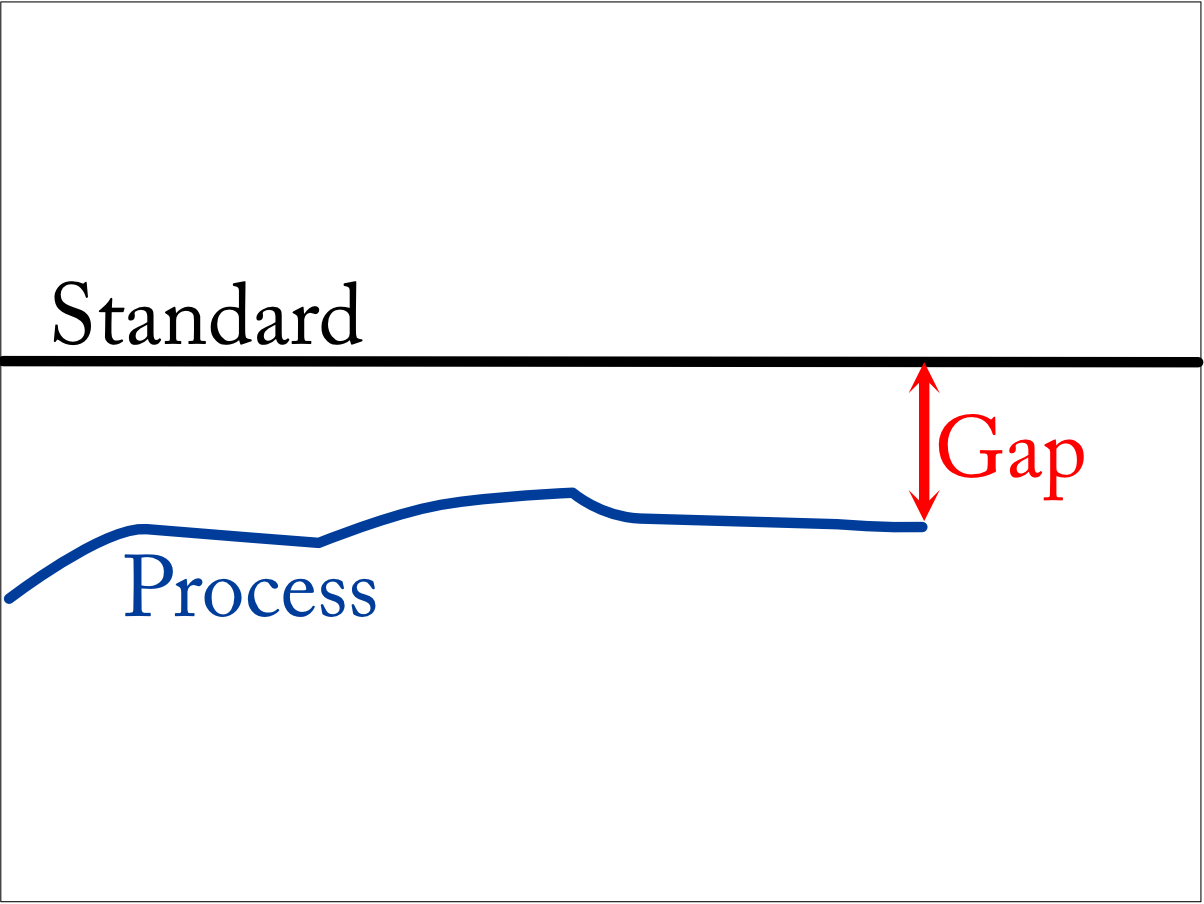
It’s the difference between your current state, and the standard you have set for that process, output or whatever.
If you’ve set a standard for something, and you’re not meeting that standard, then that’s a problem.
In Lean, problems are celebrated.
“Hey look! We can make this better!”
Too often, problems are swept under the rug. Hidden from view. “Nothing to see here.”
But what if you just don’t KNOW you have problems because you don’t know if you’re deviating from the standard? Well, that’s a problem.
You can’t improve what you don’t measure.
It’s a gap between what should be happening (you should be measuring those critical things that matter in your business and comparing them to the set standards for them) and what’s actually happening (you’re not measuring the current state to know if you’re hitting your standard, or you don’t have a standard to begin with). Read more on Standards in Business here.
Ok, let’s say you have standards, and you are meeting them. All of them. Good for you!
Does that mean you don’t have any problems? Gasp Does it mean you can never get better?
Well, no… and no…
You might have problems in places where you don’t have formal standards or aren’t actually measuring against the standards.
But, if that’s not the case, then you can still identify “Improvement Opportunities”.
These opportunities arise when you are performing to your standard, and decide you can do better. The result is that you set a new standard.
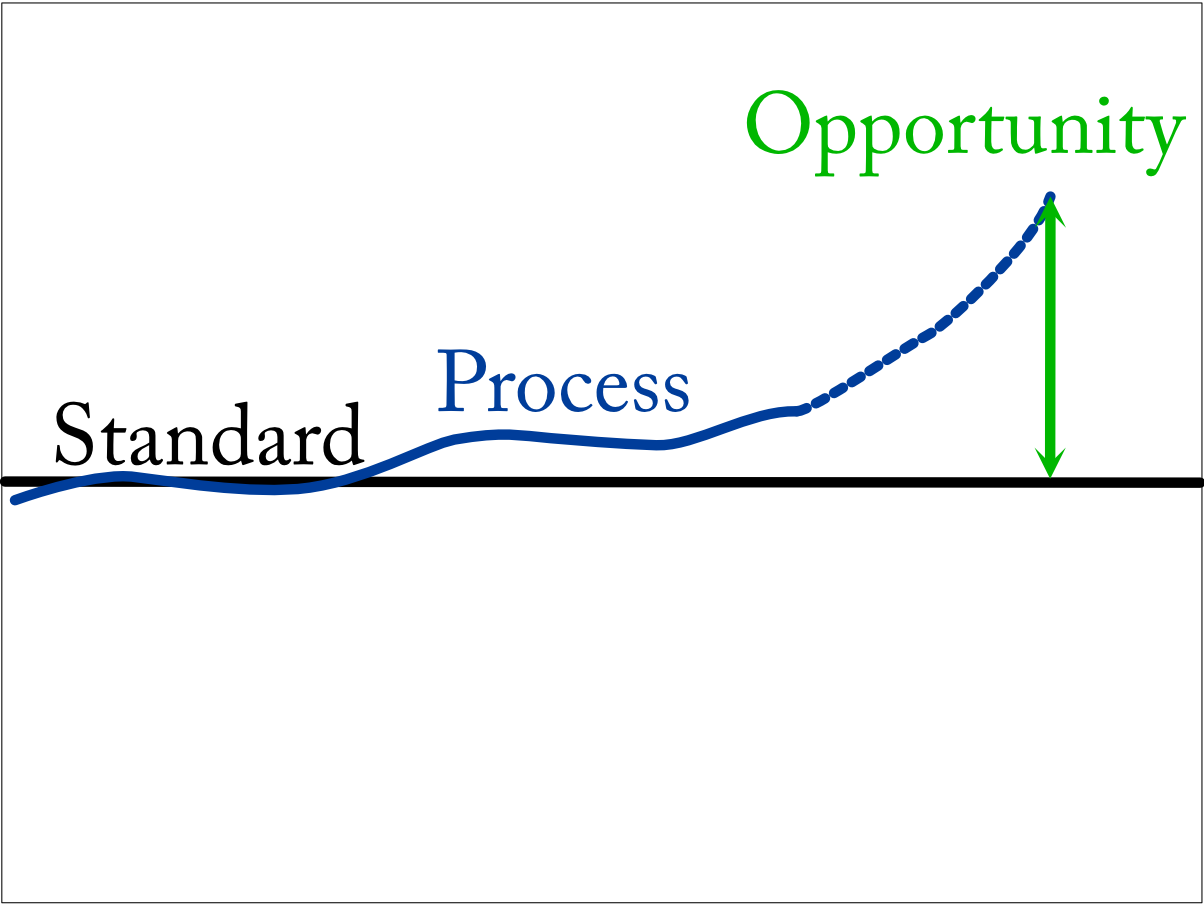
Rest assured, you can always improve.
And there’s a process for that. (Of course, there is, it’s Lean after all, and there’s practically a process for everything!)
I digress.
So, the big difference between a problem, and an improvement opportunity is that with a problem you aren’t performing to the standard, and you then have to figure out what is getting in the way – streamline the process, remove barriers, hold yourself accountable, whatever. With an improvement opportunity, you are already consistently performing to the standard, but you think you can do better, and you want to raise the standard.
One last thought.
So, why aren’t they still “problems” if you’re just raising the standard?
I think it boils down to timing. Usually, management doesn’t sit around and say “Let’s raise the standards, thereby creating problems for ourselves”.
Ok, in big corporations, maybe the management team does sit around and raise standards. Then they probably wonder why no one is meeting them. Trust me, that makes no one happy.
Usually, it’s better to say “Hey, I think we can do this better.” Let’s see how much more we can get out of the process, then raise the standard.
Incidentally, if more than one person is involved in that process, or that one person that is involved isn’t you, include them. The people that do the work are the ones that know the work the best.
Even if you wrote the procedure that they are—to the best of your knowledge—following to a T. They still know it better than you, unless you are right there with them also doing the same work with the same systems. Then they know it as well as you, and should still be part of the improvement, or problem-solving process.